Many have found a significant improvement in cutting when supplying the air assist system with higher pressure air from an external air source, usually a standard air compressor.
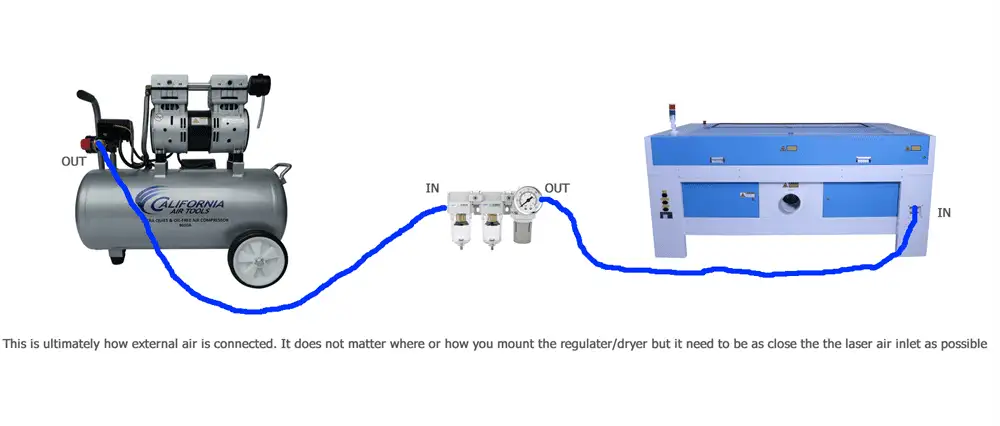
Fiber laser cutting gas
The fiber laser cutting gas is critical for keeping flare-ups at bay, mitigating smoke, helping keep the lens cleaner and cooler (it really shouldn’t get that hot if it is in proper order anyway), and, when cutting, catalyzing the ablation of material and evacuating the debris field through the bottom of the substrate and out the downdraft exhaust.
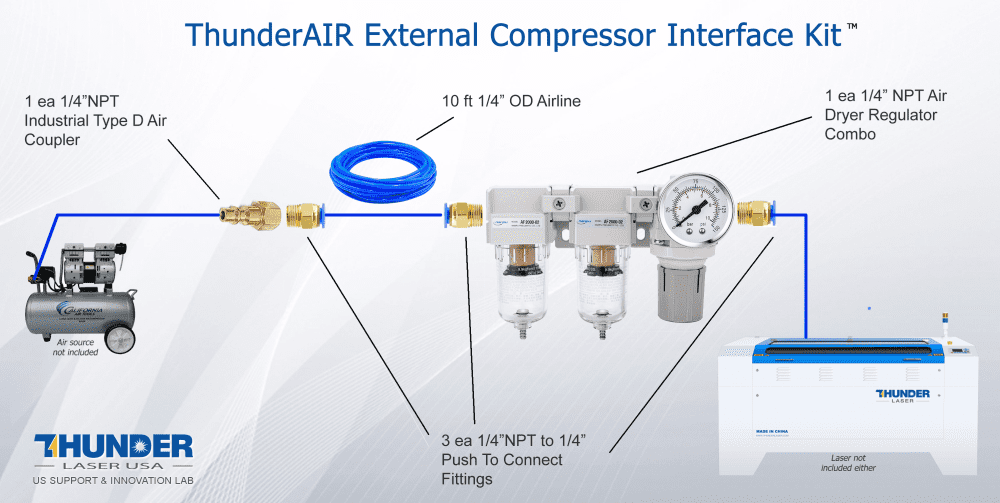
Thunder Laser Laser cutter have 2 modes for air assist. Cut and Engrave. The 2 air solenoids are controlled with the smart board. There are also 2 needle valves mounted on the front left panel so you can adjust the flow for each mode as well as momentary push buttons to test the flow. When you press a button the corresponding stage activates for 10 seconds.
What are the best fiber laser cutting gas for laser cutting?
1. Purity standards for laser cutting assist gas
Certainly, the quality of the laser generator affects sheet metal cutting. The purity of the laser gas mixture (CO2, He, and sheet metal N2 mixed in specific percentages to form a particular gas) used in the laser generator is critical. Domestic gas suppliers can only produce high purity CO2 and high purity N2. Therefore, high purity He has long depended on imports. The quality of laser cutting assist gas from manufacturers and the development of gas equipment
Firstly, there is a particular connection with the lagging development of gas equipment. Secondly, poor laser cutting gas quality and decreasing purity are hazardous factors. However, long-term use of non-compliant gases can lead to rapid aging of the vacuum glass tube in the laser generator. The slightest dust makes the laser generator cause unavoidable accidents, resulting in personal safety. The specific purity requirements are CO2 99.995%, He 99.996%, and N2 99.999%.
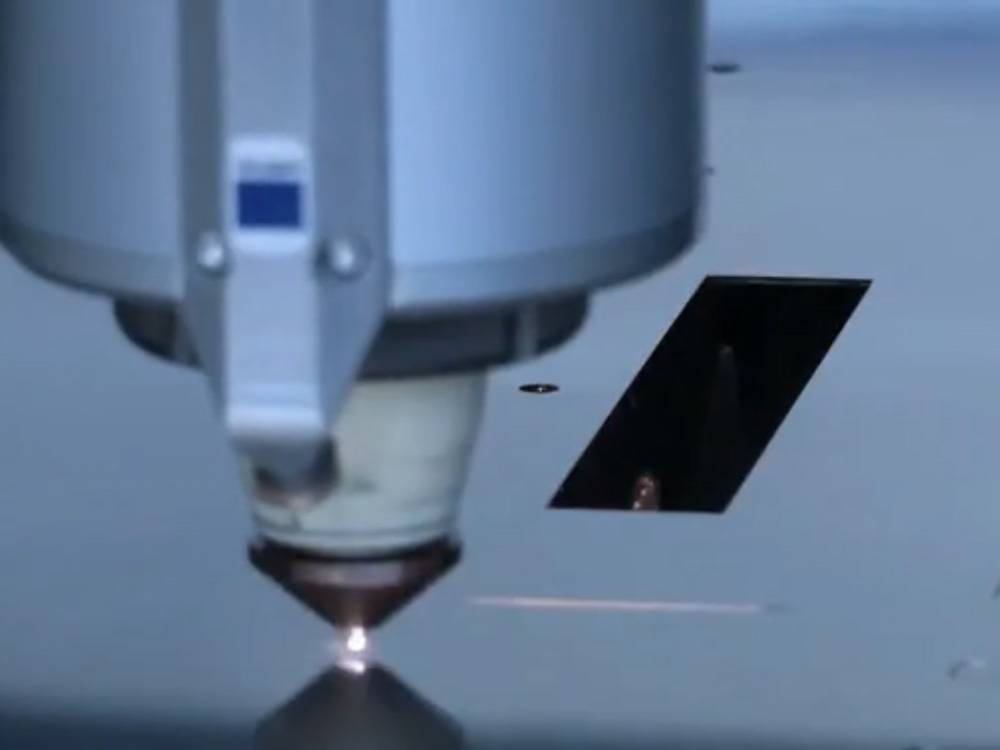
2. Consequences of substandard purity of fiber laser cutting gas
The purity of the fiber laser cutting gas in the laser cutting process directly affects the beauty of the part section. The standard additional gases are O2 for carbon steel, N2 for stainless steel, and compressed air for aluminum plates. Oxygen purity of 99.95% for carbon steel cutting section without burr, no luster. And, the oxygen purity is 99.99% for the carbon steel cutting section without burr and slight brilliance. Oxygen purity 99.999% for carbon steel cutting section without burr, good gloss.
How do we determine the oxygen impurity in cutting? Engineers can use a 10mm carbon steel plate to test. If the section is not glossy and the burr is large, we can determine that the oxygen is impure. Of course, we have to ensure that the machine parameters remain unchanged.
3. The effect of ammonia purity on laser cutters
Moreover, when the purity of nitrogen is 99.95%, there is no luster and burr in the section of cutting stainless steel. However, the area is smooth and shiny when the nitrogen purity is 99.99% on both stainless steel and aluminum plate.
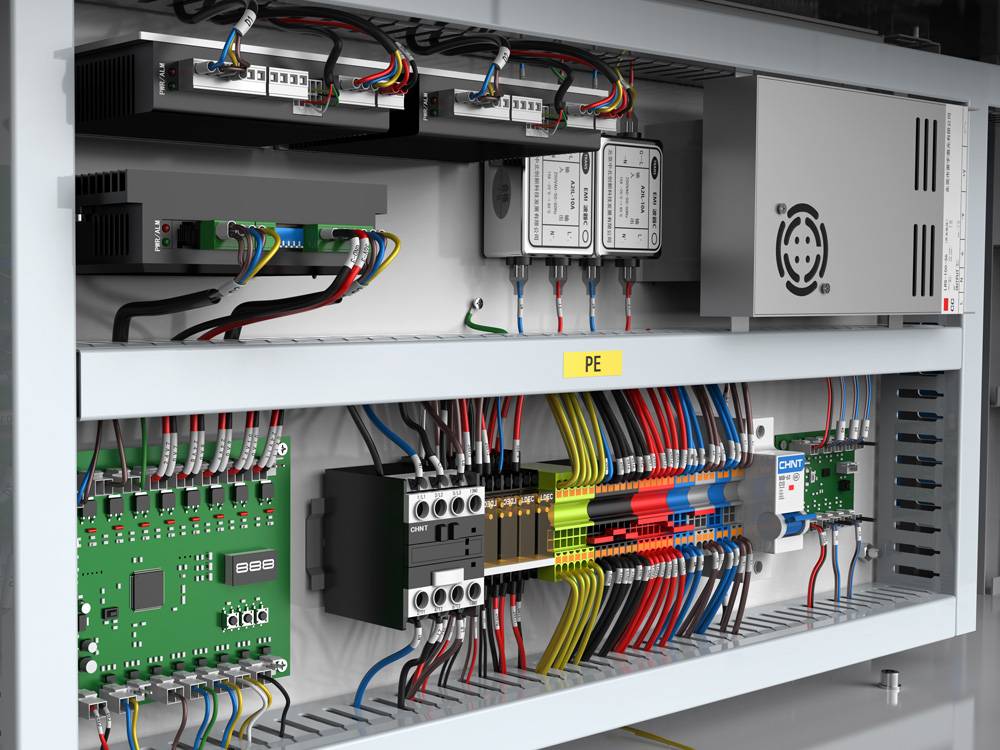
For example, an engineer can use 3mm stainless steel for testing. On the other hand, if the fiber laser cutting gas purity is not up to the standard, there will be micro burrs and burned sections. However, one thing to note, laser cutting is more sensitive to stainless steel, aluminum, and reflective materials. as a result, it is easy to cause damage to the lens. So, reducing the laser power can protect the lens. On the other hand, the supply of nitrogen should be increased.
Above all, laser cutting has a high requirement for compressed air. It is necessary to use a three-stage de-watering plus dry.
That is to say, to ensure the stable operation of the optical path system.
The guide for laser cutting system
1. Automatic electrical laser cutting system
For instance, ordinary machine control using a microcontroller should be sufficient. However, laser cutting machines have to perform complex calculations, automatically calibrate
the cutting head, and automatically exchange the platform. Therefore, the latest fiber laser cutting system is an electrical cabinet. The cabinet design defines the functions of each module.
For example, wear anti-static wrist guards inside the cabinet during maintenance. On the other hand, you should also avoid a moisture
environment. In addition, it is necessary to ensure that the cooling laser cutting system inside the cabinet is working correctly. In addition, we should often use 2Pa pressure to blow off the dust inside the cabinet
Dust. Because a small amount of dust can cause a laser cut machine to short circuit
2. Laser cutting machine optical path conduction system
After the laser is excited by the generator, it needs to be refracted by the lens to form the entire light path. Then, it is irradiated to the part’s surface to generate the laser beam. To clarify, the lenses used in laser equipment are a radiation hazard when broken. Acetone with cotton is the best choice for cleaning the lenses. But do not use alcohol. If you are cutting suddenly found parameters, no matter how to adjust can not reach a good cross-section. And the laser cutting machine also emits blue light.
At this time, it is necessary to calibrate the focus of the optical path. Pay attention to safety and wear radiation protection equipment when in school. Because the adjustment principle of each device is the same, please follow the manufacturer’s method to adjust. Just adjust each light path point to the center of the cross-tolerance deviation +0.5mm. The next cut also requires readjusting the focal length of the cutting head.
3. The mechanical laser cutting system
The laser cutting machine requires a dust-free working environment. The cutting itself generates dust. It is most appropriate to replace the dust cover every two years. However, daily maintenance is also essential. If dust gets inside the bearings and gears, it will reduce the life of the laser cut machine.
For example, cleaning and lubricating the llaser cut machine every month will increase the life span of the cnc laser cutting machine.
One of the core parts of the laser cut machine is the table exchange. Small pieces of iron left in the guide rail are enough to cause the cutting table to overturn and other safety accidents. Therefore, at the end of each work, it is necessary to clean the cnc laser cutting machine. When not working, pay attention to what foreign objects are around.
4. laser cutting machine safety protection system.
Earlier, many laser manufacturers developed the market with great success. For cost reasons, a large part of the laser equipment is no safety protection laser cutting system. As a result, laser cut machine accidents occur frequently. The root cause is the low quality of the operator and illegal operation. Laser manufacturers do not have systematic safety training for operators.
The laser manufacturers do not provide systematic safety training to operators.
We have put safety training and the development of strict daily operating rules into a book long ago. We have also installed strict safety protection systems on our laser equipment. Some customers have removed the protective doors for convenience and shielded the safety doors and their gratings directly, which can easily cause significant accidents. So the safety operating system is fundamental.
Conclusion
For some faults, you cannot fix, be sure to contact the manufacturer for repairs in the first instance. Private disassembly and overhaul are strictly prohibited.
The laser cutting machine is a set of rigorous automatic equipment. Therefore, the timely replacement of specific spare parts of the device, otherwise the whole body is involved – hair. When the ambient temperature changes, be sure to fill the refrigerant in the chiller. Frequent downtime will lead to early aging of the laser generator, so two
maintenance of the laser cutting machine every two years.
The above analysis is in the process of using the laser cutting machine and some of the problems found by our users.
These are some of the areas that do not attract much attention from users. However, it is easy to ignore these problems consequences are very serious. If you have other questions about the use of laser cutting machines, welcome to consult us.