Introduction
Laser cutting machines are currently the most advanced sheet metal processing machines. The cutting method directly determines the productivity and workpiece quality. Finding effective cutting techniques can improve production efficiency and product quality. Reducing plate waste can result in significant savings in production costs.
The principle of increased cutting efficiency
There are many ways to improve the speed and quality of cutting when using a laser cutting machine. The energy density of laser cutting machines is very high. Furthermore, the laser cutter can cut without touching the material. The laser generator emits a laser beam, which the optical path system then focuses on points with a minimum diameter of less than 0.1 mm. As the cutter moves, the laser cutter generates a high-pressure stream. These dots form a powerful cutting beam. The cutting material then absorbs the heat of the shaft, and the temperature of the cutting surface rises rapidly.
When the cutting material’s surface temperature rises to its melting point, the cutting material liquefies. Along with the liquefaction of the cutting material, cavities appear. It is worth noting that we have to add different auxiliary gases depending on the fabric. These other gases have two functions. One is that it allows the cutting material to melt more quickly. The second function is that the auxiliary gases blow away the melted slag.
After introducing the technology, CNR Cosmos has purchased a large number of laser equipment, which plays a significant role as it is responsible for more than 60% of the plate undercutting work of our various models.
Common cutting styles
The main standard undercutting methods are shearing, wire cutting, profiling, flame-cutting, waterjet cutting, and laser cutting. Among them, laser cutting has been more and more widely used in steel plates below 16mm due to the advantages of the smooth kerf, accurate size, fast speed, low noise, less smoke, and dust as well as the ability to carry out cutting of plates with various complex shapes.
We can work out many efficient cutting methods. Through experimental exploration, the following cutting techniques used in laser cutting have been summarised and, after being used in actual production, have effectively improved production efficiency and reduced material wastage.
Three common ways to improve cutting efficiency
1. Frog hopping air stroke feeds
Frog hopping is the empty stroke method of laser cutting. To help you understand this cutting method, we have drawn the following simple trajectory diagram. We generally cut A first and then B next. We can only move to B to start cutting if we close the cutting head first. The movement from point A to point B, where the machine is running “empty,” is called an empty stroke.
The general empty travel of a laser cutting machine is shown in Figure 2, where the cutting head has to complete three movements in turn: up (to a safe enough height), flat (to reach the top of point B), and down.
Saving time in the movement of the cutting head is then a critical point in improving cutting efficiency. Therefore, we can link the motions of closing the mechanism, raising the cutting head, lowering the cutting head, and finally opening the cutting head. Move the cutting head up and down towards B one at a time. When the cutting head is about to reach point B, lower the head and move it towards B. This process moves like a frog jump.
This type of air travel only takes time to move from point A to point B, eliminating the need for ascent and descent. The laser cutter’s frog-jumping feeds effectively reduce its time to move through the empty stroke, thus increasing processing efficiency.
2. Concentrated piercing
Concentrated piercing, also pre-piercing, is a machining process. This function is not commonly available on laser cutting machines. For example, the laser has to go through two stages: perforation and cutting for each contour when cutting thicker sheets. The conventional process is perforation → cutting contour 1 → perforation → cutting contour 2, as shown in the diagram, where the dots are the perforation points and the arrows are the cutting path sequence.
Centralized piercing means that all the piercing processes on the entire sheet are executed centrally in advance. We then perform the cutting process. As shown in Figure 5, the tiny dots in the diagram are the perforation points, and the arrows are the empty stroke path sequence.
The machining process route for centralized piercing is
(1)Complete the piercing of all contours
(2) Return to the starting point
(3)Cutting of all contours
With centralized piercing, the total length of the machining trajectory is increased. However, the advantage is that overburning does not occur with centralized piercing. This is particularly noticeable during the piercing of thick plates. In general, heat accumulates around the perforation point. If you cut immediately at this point, overburning can occur. With a centralized piercing process, you wait until you have finished all the piercings and then return to the starting point to cut. This avoids overburning as there is sufficient time for heat to dissipate.
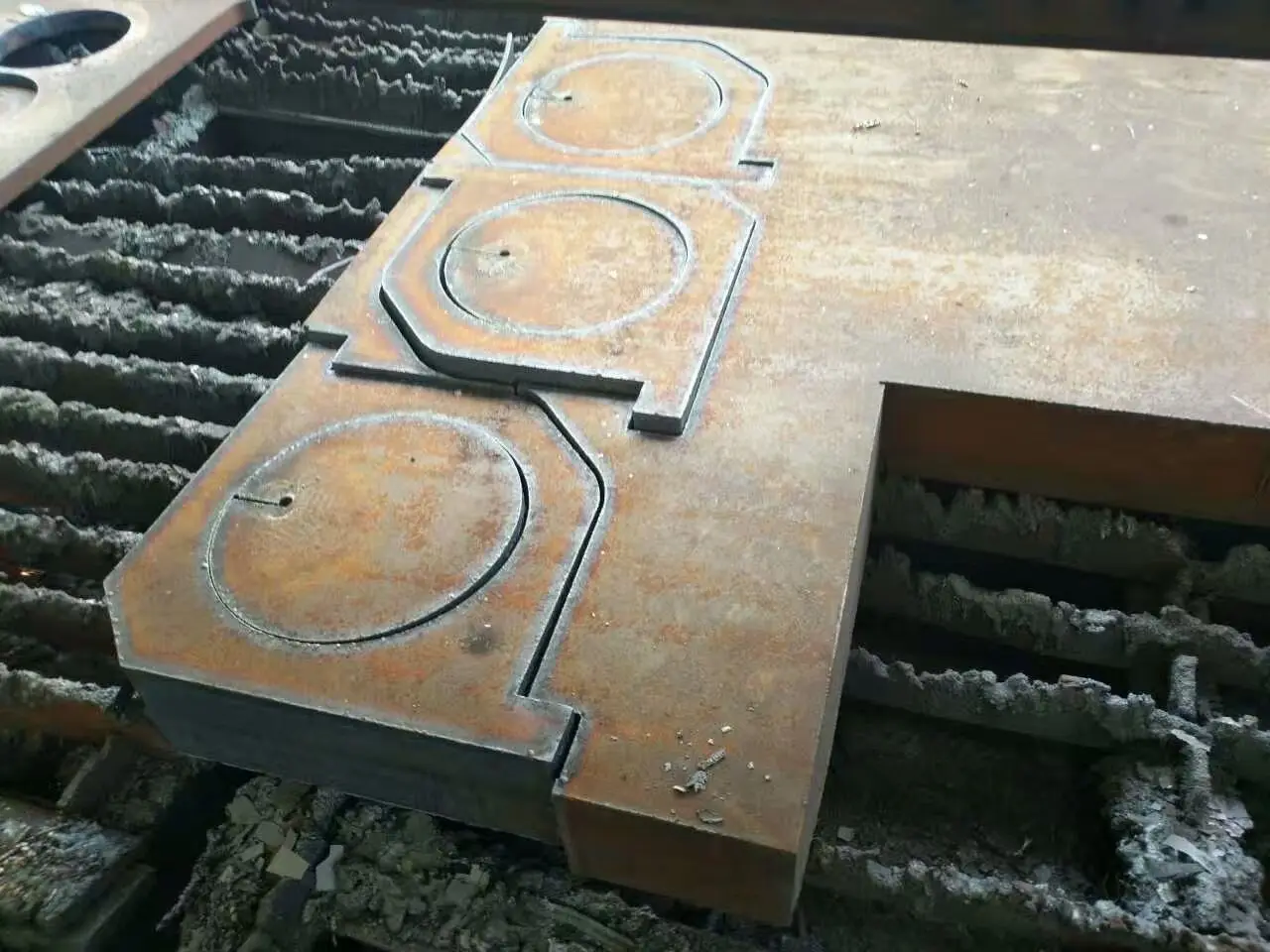
3. Applications of micro-connectivity
A serrated support bar holds the sheet when you process material by laser cutting. The part you cut off cannot fall through the gap in the support bar if it is not small enough. If the claim is not big enough, the support bar rest will not be able to drag it. So parts that are too big live too small can get out of balance, and workpiece buckling can occur. The cutting head, which is moving at high speed, may collide with the part. The consequences of a collision can range from downtime to damage.
To change this, you can use an unconnected cutting method.
When programming the laser cutting of a graphic, you disconnect the closed contour in several places. This enables the cut part to adhere to the surrounding material and not fall off. These breaks are called micro-joins. The disconnection distance is 0.2 to 1 mm. the thickness of the sheet material is large, and the disconnection distance is small. Conversely, a small thickness of the sheet results in a significant disconnection distance.
Micro-joins join the part to the surrounding material. You have to add the correct number of micro-joins depending on the length of the contour. You also have to distinguish between the inner and outer shapes so that the inner contours (scrap) that do not retain micro connections fall off. And the outer contours (workpieces) that contain micro-joins are glued to the parent material, thus eliminating the need for sorting.
Analysis of the deformation of small holes (smaller diameter than plate thickness)
Size of the cutting hole in relation to the thickness of the material:
Carbon steel plates | Cut apertures |
≤8mm | The diameter of the hole must not be smaller than the thickness of the sheet. |
≤10mm | The diameter of the hole must not be less than 1.2 times the thickness of the sheet. |
≤4mm | The diameter of the hole must not be smaller than the thickness of the sheet. |
4mm≤ | The diameter of the hole must not be less than 1.2 times the thickness of the plate. |
However, there are many instances where the hole diameter cut is smaller than the thickness of the sheet. This makes cutting more difficult, but the quality of the sheet we cut is also poor. When cutting programs are cutting thick plates, you can use the pulse perforation method. The concentrated energy then burns the sheet. So how do you solve this problem? After continuous experimentation, we have found that the fusion cutting method solves this difficulty. When you cut tiny round holes, use high-pressure nitrogen. When you cut large round holes, use oxygen.
Selection of piercing points for laser cutting processes
The laser beam forms a crater in the center after continuous irradiation of the material during the laser cutting process. The working airflow coaxial to the laser beam quickly removes the molten material, creating a small hole. This hole is similar to a wire cut threading hole, and the laser beam uses this hole as the starting point for contour cutting. Usually, the laser beam in the flight path is oriented in one direction. The tangential direction of the cut contour of the part is in the other order. They are in a perpendicular relationship.
As a result, there will be a significant change in the cutting direction of the laser beam between the time it penetrates the steel plate and the time it enters the part contour for cutting. From a direction perpendicular to the tangent line of the cutting contour to coincide with the tangent line of the cutting contour. The angle with the contour tangent line is 0 °, so it will leave a relatively rough cutting surface on the cut section of the material to be processed. This is mainly because the laser beam changes direction too quickly in a short period while moving. Therefore, it is essential to pay attention to this problem when using laser cutting to process parts.
Conclusion
In the actual production process, the operation of laser cutting machines is complex and delicate. There is a wide variety of workpieces and materials. With the increasing maturity of the cutting process, you need to use a variety of cutting techniques proficiently. And by accumulating experience in ongoing problem solving, you can improve the processing productivity of people and equipment.