How to Choose Lasers for Laser Cutting Machines?
In today’s non-metal processing field, laser cutting and engraving machines have become the new generation of productivity enhancement tools with their powerful functions and extensive applications. Within a laser machine, there is a crucial component: the laser source. It is responsible for generating and emitting the laser beam. The quality of the laser source directly relates to the performance of the laser cutting and engraving machine.
This article will delve into the working principles, processing effects, and analysis of advantages and disadvantages of three common laser sources: CO2 glass tube lasers, RF lasers, and diode lasers, providing readers with a comprehensive understanding.
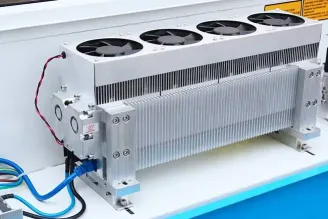
Introduction to Laser Sources
The CO2 glass tube laser has a tubular appearance. Its main components like the discharge tube, water cooling tube, gas storage tube and gas return tube are made of hard glass materials. Therefore, the CO2 glass tube laser is often simply called the “glass tube laser”.
The CO2 RF tube laser is typically abbreviated as the “RF tube” because its excitation method uses radio frequency AC excitation.
The diode laser, also known as a semiconductor laser, has a core working structure composed of a semiconductor diode material. Here we mainly discuss the blue diode laser, abbreviated as the “blue laser”.
Working Principles
Laser Generation
The working medium of a glass tube laser is a mixed gas of carbon dioxide, nitrogen, and helium gases. Laser generation generally adopts a DC excitation method, where a direct current excites the carbon dioxide molecules to transition from a low energy level to a high energy level, and then transition back to the low energy level while simultaneously emitting photons. This process is continuously repeated, ultimately outputting a laser beam of a certain intensity.
The auxiliary gases do not directly produce the laser, but rather help to improve the efficiency of the laser: nitrogen is responsible for energy transfer, promoting the rapid transition of carbon dioxide molecules from low to high energy levels; helium accelerates the thermal relaxation process, promoting the rapid transition of carbon dioxide molecules from high to low energy levels.
The working principle of the RF laser is similar to that of the glass tube laser—its working medium is consistent with the glass tube laser, but the excitation method is different: the RF laser uses a high-frequency electric field generated by an RF power source to excite the carbon dioxide gas molecules to transition and produce the laser. Here, RF stands for Radio Frequency, referring to an AC signal with a high frequency ranging from 300 KHz to 30 GHz, and does not represent its pulse frequency.
The core working principle of a diode laser is the p-n junction structure formed by the p-region (positive) and n-region (negative); when this structure receives an external DC signal of a certain intensity, electrons in the n-region are excited and overcome the boundary between the n-region and p-region, recombining with holes in the p-region and releasing photons; these photons are then amplified by the resonant cavity to ultimately produce a laser beam. In simple terms, a diode laser can directly achieve electrical-to-optical conversion. However, the current through a diode laser must exceed a certain threshold value; otherwise, the diode will behave like an LED, producing a light beam with poor coherence and weaker energy, which is not a laser beam.
Wavelength Range
The laser family includes different wavelengths such as ultraviolet, visible light, near-infrared, mid-infrared, and far-infrared lasers. For a specific laser source, the working medium and wavelength modulation/structural design determine the output of a particular laser wavelength.
For CO2 lasers, including glass tube and RF tube lasers, the nature of their working medium determines that the laser wavelength they can directly output is typically around 9-10μm. This band happens to fall within the “atmospheric window” range of 8-14μm, where the atmospheric transmittance is high and air absorption and loss of the laser is relatively low. More importantly, common non-metallic materials such as wood, plastics, and fabrics can effectively absorb light in the mid-infrared range, so CO2 lasers can easily cut and engrave these non-metallic materials. Currently, the main wavelengths of CO2 lasers on the market include 9.3μm, 10.2μm, and 10.6μm. Among them, the 9.3μm laser is suitable for processing polyimide film, polycarbonate, PET, etc.; the 10.2μm laser is suitable for processing polypropylene; and the 10.6μm laser is suitable for processing most non-metallic materials. Thunder Laser’s cutting and engraving machine series uses a 10.6μm CO2 laser source, with a wide range of applications, capable of processing wood, acrylic, ABS, paper, fabric, leather, bricks, and more. By changing the modulation frequency, it can also process special materials such as polyimide film.
However, since the CO2 laser operates in an invisible wavelength range for the human eye, it cannot be seen with the naked eye. Thunder Laser uses a focusing lens to combine the visible indicator red light with the invisible laser light path, making the CO2 laser visible. Since the indicator red light is harmless to the eyes, we can click the frame button before processing to directly observe the range covered by the moving indicator red light, confirming the area the laser will process to ensure safe and accurate processing. Please note that during laser processing, the cover must be closed for safety, and the laser should not be viewed directly.
In comparison, diode lasers have a wider wavelength range, typically between 400-2000nm. Common wavelengths used for laser processing include 532nm (green), 450±5nm (blue), and 405nm (violet). These laser wavelengths fall within the visible light range and can be seen by the naked eye. However, this does not mean that directly viewing visible lasers is safe; no matter which type of laser, they should not be viewed directly, otherwise it can damage the eyes and cause harm.
Unlike carbon dioxide infrared lasers, visible laser wavelengths do not fall within any “atmospheric window” band; in other words, under the same light path, air causes much greater loss to blue lasers than to carbon dioxide infrared lasers. The wavelengths of diode lasers can process non-metallic materials and are also suitable for metal processing, as metals can effectively absorb these shorter wavelengths of light. In particular, blue lasers are especially suitable for processing highly reflective yellow metals such as brass and gold.
Laser Light Path
Generally speaking, the longer the path the laser travels and the more reflecting mirrors used, the greater the laser loss.
In small and medium-sized laser equipment, CO2 lasers, including glass tube and RF tube lasers, typically use three reflecting mirrors to change the light path, ultimately outputting a laser beam perpendicular to the processing platform. This is because the volume of the CO2 laser source is relatively large and cannot be placed directly inside the laser head.
On the other hand, diode lasers have a very small volume and can be placed directly inside the laser head. Usually, a single laser beam only requires 0 or 1 reflecting mirror for its light path transmission.
Laser Quality
The quality of the laser beam directly determines the quality of laser processing. Laser quality is measured by parameters such as M². M² is the ratio of the actual beam to an ideal Gaussian beam. The closer M² is to 1, the better the beam quality. Intuitively, the better the beam quality, the smaller the spot size at the focal point, the higher the power density of the laser, and the higher the efficiency and precision of cutting and engraving. Additionally, the more stable the laser beam quality, the more consistent the processing effect will be for each run.
In general, within the commercial small and medium-sized laser cutting and engraving machine field, the laser beam quality of CO2 lasers is better than that of diode lasers: the M2 value of CO2 lasers is typically between 1.1 and 1.3, while the M2 value of diode lasers is typically between 1.1 and 1.7.
Firstly, the gain medium of CO2 lasers is more uniform and stable: CO2 lasers use a gas mixture as the gain medium, which is more uniform and stable compared to the semiconductor materials used in diode lasers.
Secondly, the laser structure of CO2 lasers is better designed: the design of CO2 lasers allows the output laser beam to have a better transverse mode structure, closer to the ideal Gaussian profile, while the beam quality of diode lasers is affected by their laser structure. The spot size and shape of diode lasers are closely related to their structure and operating conditions. Compared to CO2 lasers, the spot shape of diode lasers is more variable and irregular. Low-power diode lasers typically have higher beam quality, while high-power diode lasers have poorer beam quality. Therefore, commercial small and medium-sized laser cutting and engraving machines often do not use a single high-power diode laser but combine multiple low-power diode lasers to achieve a higher total output power.
Thirdly, CO2 lasers have a smaller divergence angle: the smaller the divergence angle, the more concentrated the beam energy, and the more suitable for laser cutting and engraving. The laser output by CO2 lasers is a thin, collimated beam. However, due to the unique structure and small size of diode lasers, refraction occurs at the output end, resulting in a larger emission angle of the output laser. This requires an additional prism to convert the laser beam into a parallel beam before focusing it through a lens.
Both glass tube lasers and RF tube lasers are CO2 lasers, and their beam quality is affected by factors such as cavity design, assembly precision, and beam propagation characteristics. Compared to DC-excited lasers like glass tube lasers, RF lasers can achieve a more uniform ionization process, thereby producing more stable and higher-quality laser output. RF tube lasers typically have better beam quality and smaller spot sizes, enabling them to perform very fine engraving.
Cathode Sputtering
Cathode sputtering refers to the phenomenon where, under high voltage, a plasma is formed between two electrodes, and the positive ions in the gas are accelerated and collide with the cathode, causing atoms or molecules of the cathode material to be sputtered out due to the impact. The sputtered material will deposit on other surfaces, leading to contamination of the laser cavity, loss of cathode material, changes in the electrode gap, and other issues that affect the laser’s lifespan, stability of laser output, and laser output quality.
The cathode sputtering phenomenon is more pronounced in glass tube lasers. This is caused by factors such as the cathode material, design structure, and overheating due to lack of timely cooling during continuous operation. The cathode material and packaging structure of RF tube lasers reduce the occurrence of cathode sputtering, resulting in more stable performance and longer service life.
Diode lasers typically do not involve the traditional cathode sputtering issue because their core operation is based on solid-state semiconductor materials and does not require gas as the working medium.
Processing Performance
Processing Time
The processing time for diode lasers is far longer than that of CO2 laser tubes: when processing the same product, the processing time of a diode laser is generally about three times that of a CO2 laser tube, and this is especially noticeable in cutting.
This is related to the maximum output power and maximum processing speed of the laser source. In general, for small and medium-sized laser machines like desktop models, the output power of the diode lasers used is typically 10-20W, with a few models reaching above 40W, while the maximum processing speed does not exceed 1000mm/s. In contrast, the output power of CO2 laser tubes in small and medium-sized laser machines is generally above 30W and can reach hundreds of watts, while the maximum processing speed can reach 1000mm/s or even 2000mm/s.
Higher power means that the machine can achieve the same effect at a faster speed and with fewer processing cycles.
Applicable Materials
CO2 lasers can process wood, leather, paper, cardboard, fabric, transparent and opaque acrylics, stone, glass, ceramics, anodized aluminum, and coated metals. Diode lasers can process wood, leather, paper, cardboard, opaque acrylics (black, brown, red, yellow, green), stone, coated glass, coated ceramics, stainless steel, titanium, iron, and aluminum oxide.
The main differences are:
1.CO2 lasers can directly process highly reflective non-metallic materials such as transparent acrylic, which diode lasers cannot do. To process these materials, diode lasers require spraying paint on the bottom of the material or placing a black board or black paper underneath.
2.Diode lasers can directly process bare metal materials, which CO2 lasers cannot do. To process metal materials, CO2 lasers require spraying paint on the metal surface.
3.Even for the same material, different laser sources can produce different processing effects: for example, when engraving slate, CO2 lasers produce a whitish engraving effect, while diode lasers produce a yellowish engraving effect with uneven patterns and glassy particles. Different people have different aesthetic preferences and may make different choices.
Processing Effect
Glass tube lasers have a significant cutting effect on non-metallic materials, capable of efficiently cutting paper, wood and bamboo products, acrylic, rubber, and other materials.
RF lasers perform exceptionally well in non-metallic material engraving. Their beam shaping and polarization properties enable more delicate and uniform processing effects. Beam shaping technology can adjust the shape and size of the laser spot, resulting in a more uniform energy distribution during laser processing, thereby improving processing quality and efficiency. Furthermore, the linear polarization characteristic of RF lasers helps reduce energy loss when processing highly reflective materials, increasing processing efficiency.
Diode lasers also perform well in the field of non-metallic engraving and cutting, but due to their generally lower power, they are only suitable for cutting thin materials and shallow engraving. For slightly thicker materials, multiple processing cycles are required, which can increase errors.
If you need to cut thick materials or perform deep engraving, or if you want to complete the processing in the shortest possible time, we recommend using a CO2 laser. Because CO2 lasers have higher power, they can not only cut thin materials and perform shallow engraving but can also cut thick materials and perform very deep engraving. The higher power ensures that you can achieve the same processing effect at higher speeds in a single pass.
Overall Machine
Service Life
CO2 glass tubes cannot be refilled and reused, so their service life is shorter compared to RF laser tubes, generally ranging from 2,000 to 4,000 hours. However, if the working environment is good and proper maintenance is performed, glass tubes can even last for more than 5 years. Thunder Laser provides a 1-year warranty service.
CO2 RF tubes have stable performance and do not require special maintenance. CO2 RF tubes can be refilled and reused, with a service life exceeding 10,000 hours. Thunder Laser provides a 2-year warranty.
The service life of diode lasers is approximately 10,000 hours. However, some diode lasers may not reach their rated service life. This is because the power of diode lasers is generally relatively low, and to achieve satisfactory results during operation, they often need to run at high power or even 100% power for extended periods. Prolonged high-power operation can accelerate the aging of the laser components and shorten the service life of the laser.
Reports indicate that after continuous 100% power operation for dozens of hours, the output power of diode lasers can decrease by 30-40% and cannot be recovered. This may be related to the strong temperature dependence of diode characteristics.
High-power operation can also cause the laser to generate significant heat and temperature rise, which can change the emission spectrum and threshold current of the diode.
Additionally, long-term high-power operation increases the risk of failure, affects stability, and can damage optical components.
Cooling Method
Prolonged operation of lasers can cause significant heating, leading to unstable laser output and degradation of beam quality. Therefore, laser equipment is typically equipped with a cooling system to ensure stable operation for extended periods. Glass tube lasers typically use a water cooling system to reduce the temperature of the laser tube, while RF tube lasers and diode lasers generally employ air cooling.
The advantage of water cooling is that it operates very quietly, producing almost no additional noise. It has good cooling effects and can effectively reduce the temperature of the laser, making it suitable even for high-power laser equipment. The drawbacks are: 1) Installation and maintenance are relatively complex, requiring an additional water cooling system, i.e., a water tank accessory; 2) It can be affected by freezing and frost in low-temperature environments; 3) If the cooling water becomes too hot, it cannot provide effective cooling.
The advantages of air cooling are simple installation and maintenance, with integrated and convenient removal. Since the cooling may not be as efficient as water cooling, it is mainly suitable for small and medium-sized laser equipment. The operation of the cooling fan will produce some noise, which may affect users who require an extremely quiet working environment.
To reduce the noise generated by fan cooling, Thunder Laser has designed an intelligent fan speed control board specifically for air-cooled RF tubes. This board can automatically adjust the cooling fan to operate at four different speed levels, from 1 to 4, with 1 being the lowest speed and 4 being full speed. When the machine is turned on but idle without processing, the fan runs at speed level 1. During processing, if the power is in the 0-24% range, the fan runs at speed level 1; if the power is in the 25-44% range, the fan runs at speed level 2; if the power is in the 45-64% range, the fan runs at speed level 3; and if the power is in the 65-100% range, the fan runs at speed level 4. Through this intelligent adjustment, noise interference can be greatly reduced.
Volume and Weight
For glass tube lasers, the length is positively correlated with the maximum output power. If you need higher laser output power, you need to choose a longer glass tube. This is because the length of the discharge tube represents the length of the laser medium, and the longer the laser medium, the higher the maximum output power of the laser.
High-power RF tube lasers have a larger volume compared to low-power RF tube lasers, but thanks to their more compact sealed design, the volume of RF tubes is much smaller than glass tubes. Even when choosing higher-power RF tubes, their volume increase is limited, unlike the fragile nature of glass tubes. RF tube lasers are made of metal, so they are heavier than glass tube lasers.
Diode lasers have a simple structure, high efficiency, and compact size, making them the lightest among the three types of lasers. In the field of non-metallic laser cutting and engraving machines, they are commonly used in small desktop machines or relatively simple open-frame machines.
Assembly Difficulty
CO2 laser machines are typically enclosed in a cabinet and are pre-assembled at the factory. They undergo testing to ensure the equipment can function properly, meaning customers can start using the machine immediately without the need for self-assembly. This is very suitable for users without a technical background and provides convenience for all users. For beginners or customers without a professional technical background, CO2 laser machines are easier to get started with.
In contrast, diode laser machines are often shipped as components that require self-assembly by the customer. This requires users to have a certain level of technical knowledge and hands-on ability, increasing the difficulty and time required for setup. However, for users who enjoy DIY and have an in-depth understanding of technology, self-assembling a diode laser machine can also be an attractive option, as learning and adapting to the equipment during the assembly process can be enjoyable. Additionally, diode lasers require the purchase of many optional components, such as honeycomb platforms and exhaust pumps, to achieve optimal performance. These optional components are typically included by default with CO2 lasers.
Usage Scenarios
Glass Tube Lasers
RF Tube Lasers
Compared to other laser types, RF lasers offer advantages such as compact size, easy maintenance, low operating costs, high beam quality, and long service life. Their small size makes the equipment more compact. RF tube lasers are suitable for applications that require high precision and long-term stable operation: easy maintenance, convenient integration and installation, low operating costs in the long run, and reduced operational pressure for users.
In the field of non-metallic laser engraving machines, RF lasers are preferred for their fine engraving effects. The high beam quality and long service life ensure consistent processing results and stable equipment operation. Whether on wood, acrylic, leather, fabric, or paper, RF lasers can achieve precise and clear engraving effects, meeting the demands of high-end markets.